Intelligent SAP inventory management
The Hänel lift as an integral part of the SAP-controlled manufacturing process
For manufacturing, various production resources are necessary, such as tools, fixtures, measuring devices, and test equipment. These parts are stored in shelf storages, tool cabinets, or storage lifts until usage. The up-to-dateness of stock information in the SAP system is an essential success factor for smooth manufacturing processes.
The direct SAP interface for Hänel lifts in Factory Control Center | FCTR enables the representation of the Digital Twin at the work center and comes with many advantages:
Core functions of the Hänel interface to the SAP system
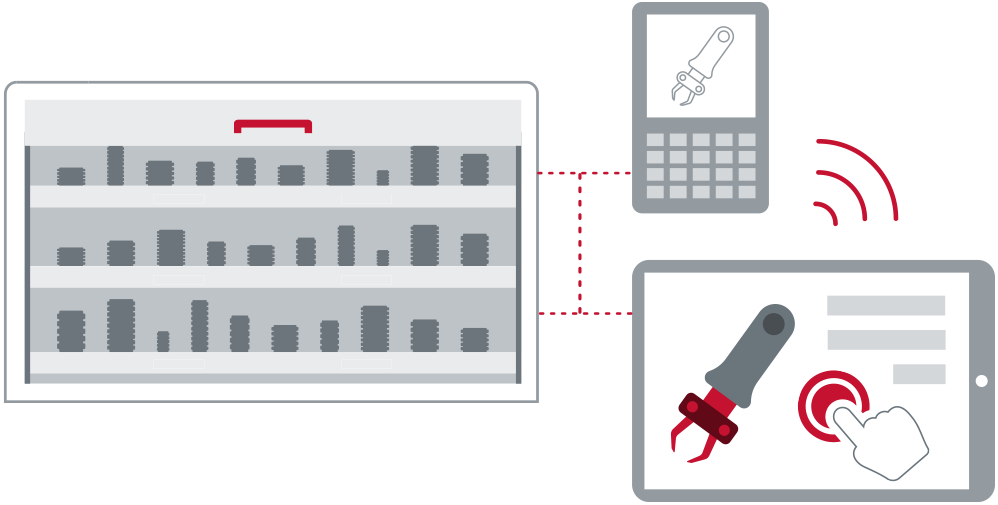
- Basic data of the material or equipment
- Stock
- Stock in other storages
- Previews and drawings
- Directly available on mobile devices or at the computer
- Direct communication between Hänel control and SAP system
- Availability check for complete tools and their components
- Display of bills of material for installation orders
- Automatic stock posting in the SAP IM module
- Optionally, automated stock posting in the SAP WM module
- Management of lift trays as storage places or functional locations
- Lift usage with an intuitive user interface on the touchpad
- Suggestion of functional locations depending on the equipment or material entered
- Notifications in case of stockout
- Simplified transfer posting masks
- Configurable search for materials in the storage
- Use of presettings for posting transactions
Functionality of the solution – according to your individual processes
- Display of planned loading and unloading lists
- Display of planned assembly and disassembly lists
- Provision of tools and fixtures
- Automatic tray movement to removal area when entering equipment numbers
- Suggestion of functional locations depending on the equipment entered at stocking
- Support of employee ID cards (separate reader necessary)
- Easy logon and logoff via ID card
- Personalized postings without SAP logon
- Automatic tray movement to removal area when clicking on storage place
- Enabling lift functions and trays via SAP authorization objects
- Execution of optimization runs
- With the SAP WM module: List of open transfer orders for goods receipt and change of storage place
- Innovative display of tray status via color encoding
- User-specific display of history for material postings
- Configurable search for materials in the storage
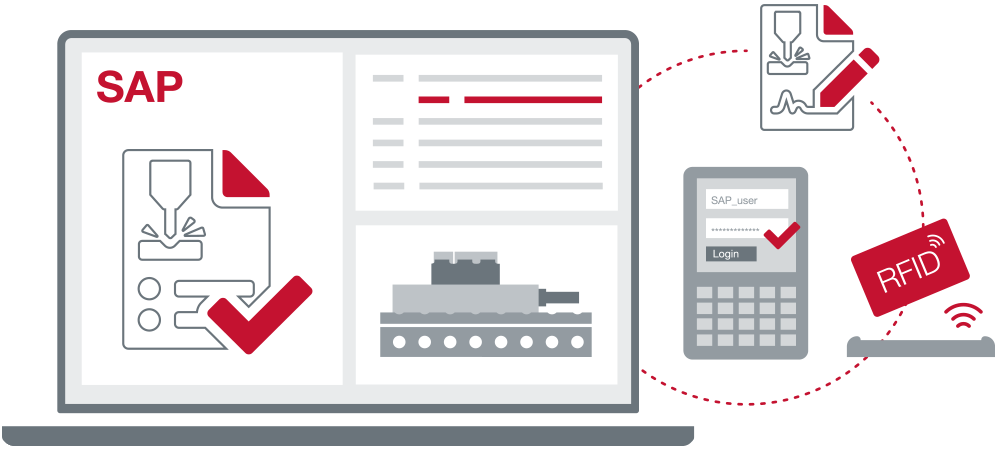